Efficient Warehouse Building: Designing for Optimal Storage
- LTM Engineering
- Jun 4, 2023
- 10 min read
To design an efficient warehouse building for optimal storage, maximizing available space is crucial. Choosing the right storage systems and utilizing vertical space for storage can further enhance the warehouse productivity. In this section on efficient warehouse building, we’ll focus on these sub-sections to help you optimize your warehouse storage and operations.
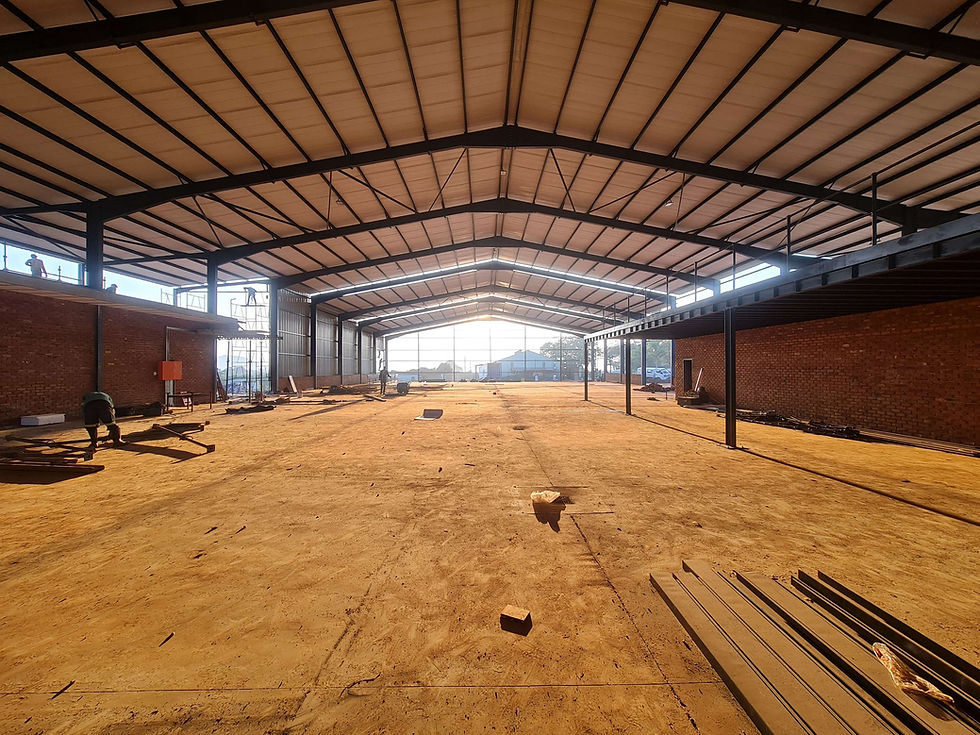
Maximizing available space
Maximizing storage space in a warehouse starts with effectively utilizing every inch of available space. This reduces the need for expensive expansions and relocations. Here's a 3-step guide:
Multi-level racking systems reduce physical footprint and increase vertical height for storage.
A well-planned layout with clear aisles and spaces between racks allows easy access and movement of goods.
Consolidate and organize stock by priority or frequency of use. Minimize movement and optimize aisle space.
Unique considerations include SKU volume, inbound/outbound flows, seasonal changes in demand, and inventory turnover. To take it further:
Modular design elements like pivoting conveyors allow for flexible warehouse design.
Reduce aisle widths based on safe operational standards.
Automation solutions, like pallet carousels or shuttle systems, reduce human error while optimizing warehouse storage density.
Planning and design are key to efficient utilization of limited floor space, streamlined workflows, and minimized overhead costs. Make sure your storage system doesn't turn into an unintentional Jenga game!
Choosing the right storage systems
When it comes to storage optimization in warehouses, selecting the right storage systems is essential. It helps with product placement and accessibility, leading to efficient operations. Here's a comparison table of different storage systems, highlighting their features and benefits.
Storage System | Features | Benefits |
Selective Pallet Racking | High-density storage with direct access to pallets. | Easy access to fast-moving goods. |
Drive-In Racking | Bulk storage for same product type. | Maximizes space & reduces aisles. |
Push-Back Racking | Stores products on inclined rails with gravity-fed carts for FIFO rotation. | Reduces aisle requirements & boosts density. |
Mezzanine Racking | Secondary floor built above existing shelving or racking. | Doubles available space without extra square meters |
Mobile Shelving Systems | Shelves mounted on tracks that slide along floor rails for easy access. | Increases capacity by reducing aisle width. |
Automated Storage & Retrieval Systems (ASRS) | Vertical lifting loaders that bring pallets from racks to workstations. | Improves storage density, speed & accuracy |
Choosing the best storage system has a huge impact on warehouse operations. While each has its own features, consider layout, space, loading docks/manufacturing lines & product types when deciding which one works best.
To make sure you're getting the best out of your warehouse space, it's important to select the right storage system.
Pallet racking systems
Professionally designed shelves are key for successful warehouse management. High-density pallet racking is one such system that optimizes storage while taking up minimum floor space. It not only maximizes the available area but also boosts safety in the warehouse.
You must pick a rack that will bear the load and make sure it's properly set up. An unreliable storage system may lead to accidents and lower work productivity. Invest in a dependable racking structure, and reap the rewards of an efficient warehouse! Tetris taught us that a great storage system leads to success.
Shelving systems
Shelving Structures: A Closer Look.
The perfect shelf system is essential for the best storage in a warehouse. Here are 3 main points to ponder:
There are various types of shelving structures, such as static, mobile, and pallet racking systems. Each has their pros and cons.
The shelf system should address the warehouse's needs. Things like load weight capacity, ceiling height, and floor space available.
Installing a quality ventilation and fir extinguishing system is necessary for safety with static shelving systems.
It's important to remember that the right shelf system can make all the difference in maximizing warehouse storage.
Warehouses have individual needs, for example some require more vertical space if they manage large items that need stacking. Looking at these differences is key when choosing shelving structures.
Recently, a warehouse had a disaster. Support pillars were not used correctly during setup which caused a collapse of the whole racking structure. Luckily, no one was hurt but this shows why proper research and selection is important when choosing a shelf system for a warehouse environment.
Why not get a robotic arm to do the hard work instead of human movers? This is the future of warehouse storage.
Automated storage and retrieval systems
Automated systems for storage and retrieval are an important part of efficient warehouse design. These systems bring many benefits, such as increased productivity, faster processing times, and improved accuracy.
Although there is an initial investment required to implement an automated system, it leads to long-term cost savings due to improved efficiency.
The type of goods stored or handled and available floor space are some of the main factors to consider when optimizing warehouse design.
Furthermore, 2020 saw a projected global warehouse automation market size of $30 billion by 2027 due to high demand for automation across industries.
To maximize storage efficiency, vertical space should be utilized as much as possible, similar to a game of Tetris.
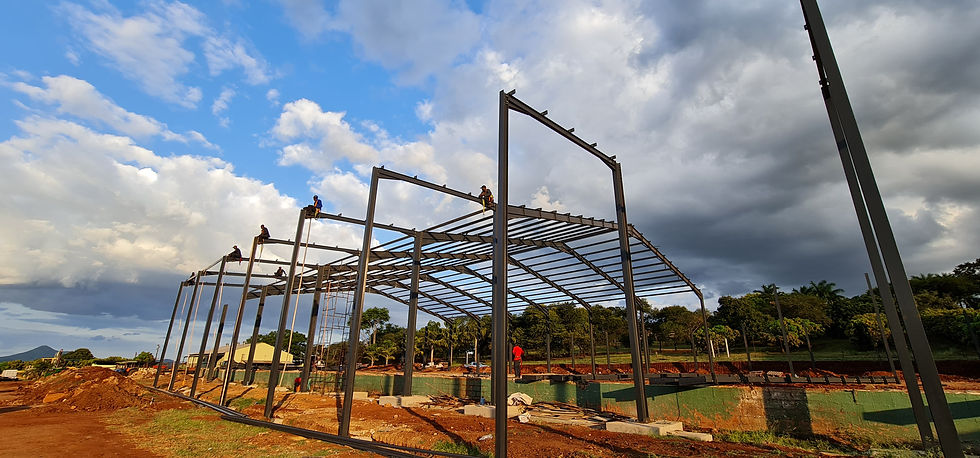
Utilizing vertical space for storage
Maximize your warehouse's potential with innovative approaches! Utilizing vertical space can free up floor space and improve productivity. Invest in racking systems that withstand heavy loads and offer adjustable shelves for customized storage. This is especially useful when storing non-perishable goods or bulky items.
In addition, factor in lighting, flooring, and ceiling height. Automated inventory management systems optimize inventory placement for further efficiency. Amazon is a great example of successful implementation of these techniques - they managed to reduce product retrieval times significantly with advanced automation technology.
Building a warehouse is like a game of Tetris - the goal is to fit everything perfectly but you never have the right-shaped piece when you need it!
Efficient Warehouse Building: Designing for Optimal Operations
To ensure optimal operations in your warehouse building, designing it efficiently is crucial. This involves creating efficient material flow, implementing effective inventory management, and designing for safety and ergonomics. By utilizing these sub-sections as solutions, you can maximize your storage capacity and enhance your warehouse's overall productivity.
Creating efficient material flow
Optimizing the movement of materials within a warehouse is essential for maximum efficiency. Design and implement a system to move goods in and out with ease, to lower costs and handling time.
Take a look at the following table to see factors that contribute to ideal material flow in a warehouse:
Factors | Description |
Layout | Design the warehouse for smooth traffic flow. This helps workers move products quickly. |
Automated Systems | Use cutting-edge machinery like conveyor belts and automated storage and retrieval systems. This will reduce manual handling and increase productivity. |
Order Picking & Shipping Method
| Choose a picking method that ensures products are packed correctly. Consider shipping methods for swift deliveries.
|
Inventory Management System | Have an effective inventory management system. This will provide accurate visibility into stock levels and help avoid lost sales. |
Remember, the structure you choose will depend on the data analysis of your current situation.
Creating efficient product flow is vital for businesses of any size. Over time, industries have improved their supply chain processes, leading to faster growth and better ROI. Less travel time means more time to pretend to be busy while avoiding actual work.

Minimizing travel time between storage areas
Maximizing warehouse efficiency requires reducing time spent travelling between storage areas. Moving items takes up a huge chunk of the warehouse's expenses. Optimizing this travel can help save costs and boost productivity.
Here are 3 tips to lessen travel time:
Analyze Data: Gather, assess, and interpret info to spot the most frequently used products. Then, place them close to order picking zones.
Set Aisle Widths: Choose the ideal aisle widths that make navigating simpler for employees and reduce space between aisles.
Exploit Tech: Use tech like automation, RFID tagging, or barcoding to improve pick-and-place operations.
Think about utilizing vertical space in your facility by designing taller shelves or installing mezzanine structures. This adds more storage space without using extra floor area.
To enhance warehouse optimization, consider using cross-docking practices. Segregate incoming inventory into outbound freight with minimal handling to quicken shipment times. Plus, use equipment such as conveyor belts or lift trucks to cut down walking distance and strain for employees for more efficient workflow.
Order picking is like a game of Operation. One wrong move and you'll hear more than just a buzzing sound!
Streamlining order picking processes
Efficiently managing the order picking process is key for optimal warehouse performance. Here's how to make it happen:
Install an inventory system that precisely tracks and manages stock levels.
Design a layout to reduce travel time, avoid congestion and boost efficiency.
Employ technology such as barcode scanners or voice-picking to speed things up.
Train and incentivize employees to be more accurate and faster.
Analyze data to find improvement areas and make adjustments.
For even better results, look into batch picking, zone picking, or wave picking. These techniques can lower travel time and errors.
Implementing effective inventory management
For maximum warehouse efficiency, an efficient inventory management system is essential. This means tracking inventory levels precisely, reducing waste, making product movement smoother, and using space optimally.
Strategies to do this include:
Employ accurate, reliable tech to track inventory in real-time
Order only what's needed, and store products properly
Audit stock regularly to minimize excess inventory and optimize space
Analyze data to determine optimal storage locations for products
Conduct regular staff training to ensure efficient practices
Monitor vendor performance metrics if relevant, to assess supplier reliability.
Knowing which products sell well helps align stock quantities with demand patterns. This guarantees fast-sellers are always in stock, and slow-sellers don't take up space.
One unique way to optimize inventory management is by using RFID tags. This cuts down on manual counting, so workers can focus on more crucial tasks.
One company was losing 10% of its monthly revenue due to warehouse problems. But, with strategic planning and the measures above, they regained control. Delivery times improved, and losses decreased thanks to precise inventory tracking. And, no more pen-and-paper guesswork!

Tracking inventory levels
Optimizing warehouse operations requires efficient inventory management. Tracking inventory levels accurately is key to reducing stock errors, boosting efficiency and lowering operating costs.
To simplify the inventory management process, a tracking system should be put in place. This system records the incoming and outgoing stock accurately. This data can then be studied to figure out reorder points and prevent overstocking or stockouts.
Automated tracking methods, such as barcoding, and using real-time data analysis tools can be used to optimize warehouse operations and enhance productivity. No more wandering around a warehouse looking for that one item! Inventory management software is the answer!
Optimizing picking routes with inventory management software
Warehouse efficiency is key for optimal ops. Achieving this? Optimize picking routes! Inventory management software can help.
Factors to consider:
Accurately tracking inventory
Pick priority
Order batching
Optimizing warehouse layout
Group orders with similar products. Determine items to be picked first based on priority.
Pro Tip: Heat mapping tools can identify high traffic areas. This allows further optimization of picking routes. Avoid acrobatics in the warehouse!
Designing for safety and ergonomics
Creating an efficient warehouse is key. Safety and ergonomics should be prioritized. Building layout, storage systems, and equipment placement should be carefully considered - this reduces potential hazards and the risk of injury or strain.
Materials and equipment must be easily accessible. Stretching or bending motions must be avoided. Lighting and ventilation are also important factors. The right design principles and training help reduce the likelihood of workplace accidents.
Safety practices have a direct impact on workers' health, agency performance, and efficiency. They can lead to increased profits. By providing safe working conditions, organizations can retain staff and elevate productivity. Maximum success in operations is achievable.
For warehouse efficiency, proper environmental conditions are key. Bright and even lighting should be installed at ground level where most activities take place. Natural light is ideal, but artificial light can be used too - with no glare or shadows. Ventilation should circulate fresh air and control temperature, humidity, and air quality - creating a comfortable working space. Insulation of walls, windows, doors, ceiling, and roof will prevent heat loss/gain, and reduce noise.
Ergonomics are important too. Adjustable desks and chairs reduce stress on workers' muscles for better performance. Office areas should be separate from manufacturing areas to reduce distractions and protect from hazardous work environments.
Smart lighting controllers regulate lights depending on usage, saving energy when not in use. Translucent panels in roofs/screens let in natural light and save energy. All of these improvements make for an efficient working environment for employees and equipment, leading to optimized warehouse operations.
Ergonomic workstation design
Designing workstations in a warehouse is important for efficiency and safety. Place equipment, tools and supplies in a way that works for tasks. Tailor height, reach and seating to match employee measurements. This will minimize strain and maximize comfort. Make aisles wide enough so workers can move around easily.
Workstation design has been updated, with advances in consumer demand and technology. Less physical labour is needed due to automation, like robots. Cost-cutting measures should not put employees at risk. Build an efficient warehouse without breaking the bank!
Cost-Effective Strategies for Efficient Warehouse Building
To achieve optimal storage and operations in your warehouse building project, you need to focus on cost-effective strategies. The following sub-sections will be the solution to designing an efficient warehouse building: Choosing sustainable building materials, Incorporating energy-efficient technologies, and Implementing ongoing maintenance and repair plans.
Choosing sustainable building materials
Go green with your warehouse building! Opt for eco-friendly and long-lasting construction materials. Such as recycled steel and concrete. These materials are renewable, energy-efficient, resist decay and weather extremities. Making them a cost-effective option with long-term benefits.
Sustainable building materials also reduce carbon footprints in the environment. Use products that conserve natural resources, over traditional construction methods. Also consider the material transportation distances. When selecting options from local suppliers to avoid excess energy consumption.
Renewable energy sources such as solar panels or geothermal heating help in efficient warehouse management practices. Use environmentally conscious designs like skylights or clerestory windows. That allow natural light into the building. Reducing the need for artificial lighting during regular business hours.
Sustainable materials have a longer lifespan compared to non-renewable elements like wood treated with pesticides. They also enable economies of scale while creating team solidarity amongst workers. Why waste energy when you can save it and use it to power your forklift races?
Incorporating energy-efficient technologies
Incorporating sustainable energy tech is essential for constructing cost-effective warehouses. Implementing innovative energy-saving systems reduces operating costs and environmental impact. Developing energy management strategies and deploying energy-efficient equipment, like high-efficiency lighting, renewable energy sources, and aesthetic coolers, optimizes warehouse ops by decreasing electricity bills and improving performance.
Traditional insulation techniques, plus advanced ones like cool roofing materials, natural ventilation solutions, and heat recuperation devices, enhance the efficiency of warehouses. Cool roofs have a reflective coating that reflects sunlight - reducing internal temp and lowering cooling costs. Employing wind-catchers as an alternative to HVAC systems provides fresh air and cuts heating costs. Maximizing natural light eliminates the need for fluorescent lights.
Large-scale solar arrays can provide cheap electricity in sunny locations with gov't subsides while utilizing unused roof space.
Energy-efficient technologies are now essential for green growth, saving substantial amounts at the same time.
Don't wait until the roof collapses - solid maintenance plans are key to a warehouse that doesn't fall apart.
Implementing ongoing maintenance and repair plans.
Maintaining and fixing the warehouse regularly is vital for its successful running and durability. A plan that guarantees constant maintenance and repair is indispensable for a competent warehouse. Here are some key points to consider when creating such plans:
Regular check-ups should be done to detect possible issues, which can then be dealt with before they become critical.
Scheduling maintenance tasks based on priority, with more important areas getting attention first.
Hire professionals who know warehouse systems and have experience in keeping them.
Regularly modify the maintenance plan as per changing needs of the warehouse.
It's essential to make sure all parts of the warehouse are well maintained and fixed. Ignoring any part may cause huge problems later.
Also, making sure workers obey safety protocols during maintenance tasks or moving heavy equipment is vital. This will reduce accidents, lower injury risk, and likely delays in operations.
For instance, one company ignored regular repair needs since everyone was too busy concentrating on new projects. But the negligence eventually caused a disastrous accident that not only slowed down operations but also caused serious financial loss. Consequently, executing an efficient ongoing maintenance plan can save time and guarantee smooth long-term running of a warehouse.
Frequently Asked Questions
Q: What are the key considerations in designing an efficient warehouse?
A: The key considerations include the layout of the warehouse, the types of storage systems to be used, the material handling equipment, and the management of inventory and logistics.
Q: How can I maximize storage space in my warehouse?
A: You can maximize storage space by using vertical shelving, optimizing aisle widths, using racking or shelving systems that are adjustable, and using automated storage and retrieval systems.
Q: What is the role of technology in warehouse design?
A: Technology plays a key role in warehouse design by offering automation, real-time inventory management, barcode scanning systems, and conveyor systems to facilitate material handling and order fulfilment.
Q: What are the most common types of warehouse storage systems?
A: The most common types of warehouse storage systems include pallet racking, cantilever racking, industrial shelving, and mezzanine systems.
Q: What are the benefits of an efficient warehouse?
A: The benefits of an efficient warehouse include increased productivity, lower costs, improved customer service, and better inventory management.
Q: How can I incorporate sustainability into my warehouse design?
A: You can incorporate sustainability into your warehouse design by using energy-efficient lighting, installing solar panels or other renewable energy sources, utilizing automation to reduce energy consumption, and implementing a recycling program.
Comments